Life cycle assessment (LCA) is a standardised method for evaluating the environmental impacts of a product or service throughout its entire life cycle. The International Organisation for Standardisation (ISO) has standardised the guidelines for conducting LCAs.
Publications of life cycle assessments have increased 30% annually since 2010, highlighting the rising importance of LCA as companies face growing pressure from consumers, regulators, and stakeholders to demonstrate sustainability and reduce their environmental footprint.
This glossary will cover the definition of LCA, how to conduct one, its benefits, regulatory requirements, which companies should conduct LCAs, and how to communicate LCA results effectively.
What is a life cycle assessment?
Life cycle assessment is a systematised method for compiling and evaluating a product or service's inputs, outputs, and potential environmental impacts throughout its life cycle. LCAs can cover a product’s life cycle from raw material extraction through manufacturing, packaging, use, and disposal.
While LCA considers various inputs and outputs, inputs generally include materials, natural resources, and energy consumed. Common outputs include waste and emissions released into the environment.
Companies and organisations can gain valuable insights from life cycle assessments, which aid in identifying opportunities to improve environmental impact, optimise product design, and inform strategic decision-making.
Because life cycle assessments align with corporate sustainability goals and regulatory compliance, understanding this process is essential for sustainability teams, C-level executives, and finance leaders.
The ISO has produced specific international standards on life cycle assessment. ISO 14040 describes the “principles and framework for LCA”, and ISO 14044 further elaborates this process and “specifies requirements and provides guidelines” for LCA. Companies interested in LCA should familiarise themselves with these standards.
Types of LCAs (cradle-to-grave, cradle-to-gate, gate-to-gate)
A life cycle assessment can either consider the impact of the entire life cycle of a product/service or focus on specific stages of the life cycle. This is the scope of the LCA.
Some examples are:
- Cradle-to-grave assessment: Assesses the entire product life cycle, including extraction of raw materials, manufacturing and packaging, distribution, use and disposal. It provides a comprehensive view of the product or service’s environmental impact.
- Cradle-to-gate assessment: Evaluates the environmental impacts of a product within a more limited scope–from the extraction of raw materials (cradle) to exit from the production facility (gate).
- Gate-to-gate assessment: This analysis analyses specific processes within the production chain. It considers environmental impacts from the start of manufacture (entry gate) to the end (exit gate). It does not account for the extraction of raw materials or product use and disposal.
Life cycle assessment vs Product environmental footprint
Given the proliferation of numerous assessment methods, the European Commission has proposed the Product Environmental Footprint (PEF) method to standardise and harmonise the calculation of product environmental impact.
This PEF method is based on the LCA, and the two share a standard cradle-to-grave scope and four-phase procedure. Like the LCA, PEF considers a broad range of environmental impacts, including climate change, ozone depletion, human toxicity, land use, etc.
PEF differs in its additional requirements for modelling material flows, emissions, and waste streams, its system of categorising products into product groups with specific category rules for calculating and comparing data, and its stricter requirements for data quality.
A limitation of PEF is its narrowly defined product categories, and product category rules exclude some products and services. Conducting this PEF could be more complicated for those whose product/service does not fit into an existing product category.
How do I conduct a life cycle assessment?
A life cycle assessment (LCA) typically involves four main phases: goal and scope definition, inventory analysis, impact assessment, and interpretation.
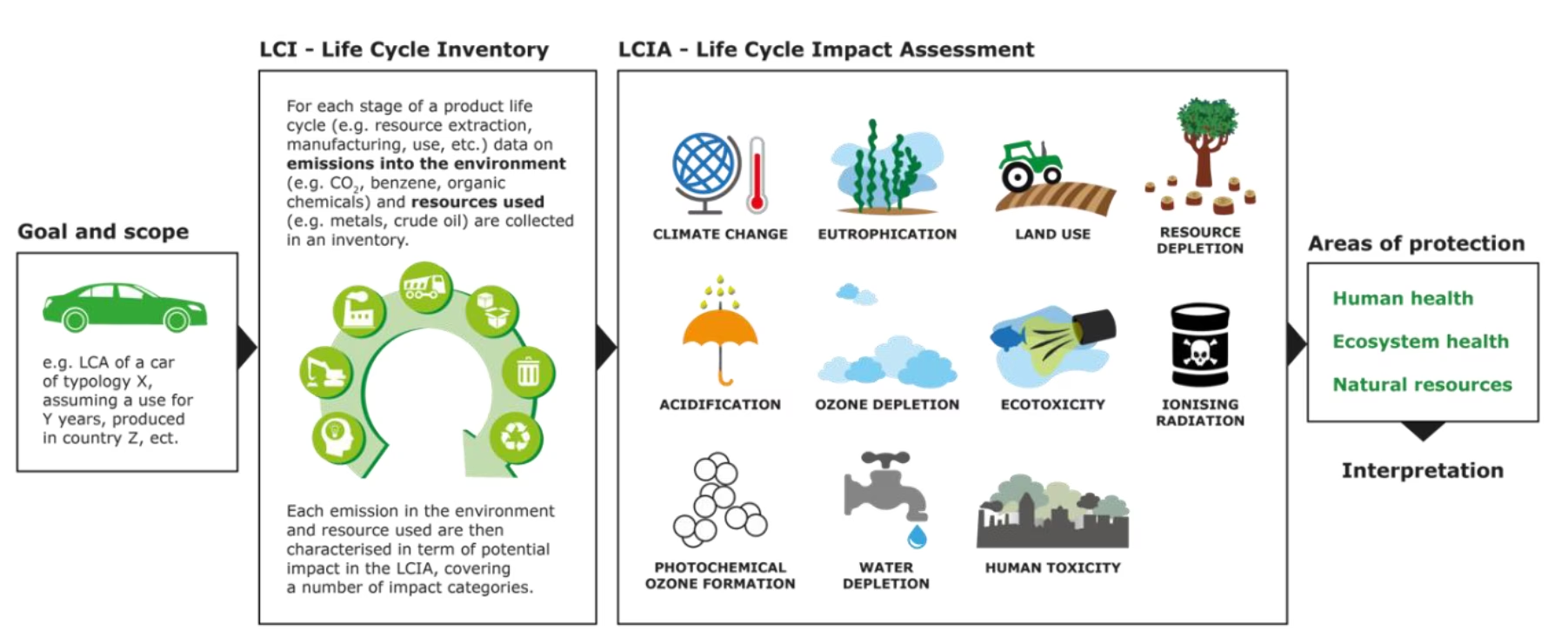
Source: European platform on LCA
- Goal and scope phase: The first phase of LCA is the phase in which goals, reasons for the assessment, and methodological choices are made. Decisions on data quality requirements, impact categories, functional units, models, system boundaries (including scope), and allocation procedures are also made.
- Life cycle inventory (LCI) phase: The second phase of LCA in which data on energy and material inputs and emissions outputs are collected and quantified. Inputs and outputs relate to energy use, raw materials/physical inputs, products, waste, emissions, and other environmental aspects.
- Life cycle impact assessment (LCIA) phase: This is the third phase of LCA, in which results from the previous inventory phase are connected to environmental impact indicators and categories. Emissions are classified into impact categories such as climate change, ecotoxicity, and ozone depletion and converted to standard units, allowing for comparison.
- Life cycle interpretation phase: The fourth and final phase of the LCA in which results from the two previous phases are interpreted given the goal and scope of the LCA, as determined in phase one. This step identifies possibilities for adjusting production choices to reduce environmental harm.
Thorough and accurate data collection is crucial and ensures the accuracy and reliability of the assessment. Companies can leverage insights to make environmentally beneficial adjustments.
Additionally, stakeholders must be engaged throughout the process to gather data and insights into a product's life cycle. Suppliers can provide data on materials, while customers can provide data on product use and disposal.
What data will I need to conduct an LCA?
Conducting LCAs requires both primary data from specific processes relevant to the lifecycle of the product/service as well as secondary data from literature or databases. This data is collected during the LCI.
Primary data concerns processes within the company’s control, including activity-based data like energy consumption. It also includes emissions data measuring the quantity of pollutants released into the environment. Secondary data from external sources, including life cycle databases, industry reports, and academic literature, fill in gaps where specific data isn't available.
Compiling accurate, high-quality data of various types and sources is fundamental to creating a detailed inventory that effectively paints a picture of a product's environmental impact across its entire life cycle.
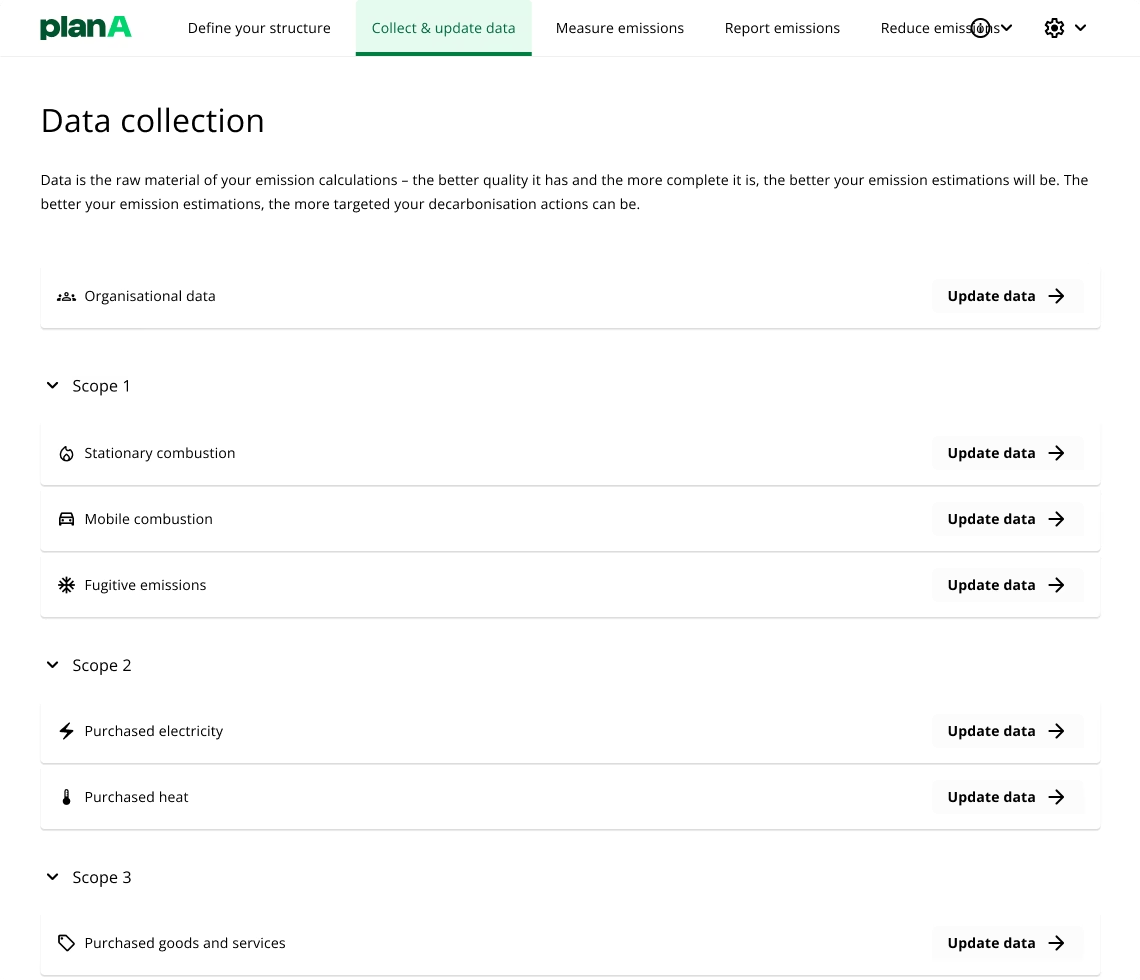
Credit: Plan A
What tools can I use to conduct an LCA?
Various tools and software commonly used in LCA include GaBi, SimaPro, and openLCA. These tools facilitate data collection, impact assessment, and reporting, making the LCA process more efficient and accurate. Technology can be a vital resource for conducting LCAs due to their complexity.
Some commonly used tools include:
- GaBi: A comprehensive software tool that allows users to model and analyse the life cycle of products, providing access to an extensive database of life cycle inventory data.
- SimaPro: A widely used LCA software that supports the analysis of environmental impacts and provides various databases and methodologies for different industries.
- openLCA: An open-source software that offers flexibility and transparency in LCA modelling, allowing users to create custom databases and methodologies.
Who are the stakeholders when conducting an LCA?
Conducting an LCA involves internal teams (e.g., sustainability, R&D) and external partners (e.g., suppliers, customers).
Internal stakeholders include teams such as sustainability, research and development (R&D), and product management, which are crucial for defining the LCA's goals, collecting data, and interpreting results.
Engaging stakeholders helps ensure that the LCA is comprehensive, reflects real-world practices, and fosters collaboration towards sustainability goals.
What are the benefits of a life cycle assessment?
Conducting an LCA provides companies with many benefits, the most important of which is a comprehensive understanding of their environmental impacts, enabling them to identify areas for improvement.
Life Cycle Assessments (LCAs) empower businesses to do more than measure impact—they redefine how products are made and used. By mapping out environmental footprints from raw materials to disposal, companies uncover untapped opportunities for innovation, efficiency, and alignment with consumer demand.
Plan A
Major benefits of LCA include improved efficiency, business advantages like cost savings, and enhanced transparency. Additional benefits include:
- Ensuring regulatory compliance: LCA is required by some environmental regulations and governments in specific contexts. In this scenario, conducting an LCA would be necessary to adhere to environmental laws and avoid legal penalties.
- Branding benefits: Changes implemented based on LCA results and effective communications of environmental impacts can improve brand image and appeal to environmentally conscious consumers. Reporting the information gleaned from conducting an LCA can garner eco certifications.
- Innovation capacities: LCA helps drive innovation in product design and processes.
Is it mandatory for companies to conduct LCAs?
To determine whether LCAs are mandatory, specific guidelines must be considered according to country, product, organisation, and industry. Regulations and guidelines constantly evolve, so staying abreast of the regulatory landscape is necessary.
One significant benefit of LCA is that data calculated in this assessment can be integrated into other reporting requirements. In the European Union, implementing LCAs can help manage environmental impact data to comply with the Corporate Reporting Sustainability Directive (CSRD requirements).
The European Green Deal and evolving global regulations signal a future where LCAs are non-negotiable. Businesses that act now position themselves as leaders, not followers. Plan A equips companies to embrace this shift with clarity and precision, transforming compliance into a competitive edge.
Which companies should conduct LCAs of their products?
Companies and industries with significant environmental impacts or those seeking to improve their sustainability credentials should consider conducting LCAs. Manufacturing, construction, food and beverage, and textiles are examples of industries with significant environmental impacts.
The fashion industry is one of the most polluting industries globally, and more than 70% of fashion emissions come from energy-intensive raw material production, preparation and processing, and other upstream activities. LCAs can identify hotspots in a company’s value chain to bring about changes like sourcing raw materials in a less environmentally harmful way.
LCAs can significantly benefit businesses aiming to enhance their sustainability credentials, comply with regulations, or respond to consumer demand for transparency and eco-friendliness.
Communicate the results of your product LCA
Following an LCA, effectively and transparently communicating results to stakeholders, including consumers, investors, and regulatory bodies, is vital to building trust and demonstrating commitment to sustainability.
By openly sharing LCA findings, companies can demonstrate their commitment to responsible environmental practices and sustainability, enhancing reputation and competitive advantage.
Communicating to B2C customers
Some strategies for effectively communicating LCA results to consumers include product labelling, marketing campaigns, and sustainability reports.
- Product labelling: Use clear and informative labels highlighting the product's environmental impact, including LCA results, to help consumers make informed choices.
- Marketing campaigns: Incorporate LCA findings into marketing strategies to showcase the company's commitment to sustainability and differentiate products in the marketplace.
- Sustainability reports: Regularly publish comprehensive sustainability reports that include LCA results, goals, and progress to keep consumers informed and engaged.
Transparency is no longer optional—it's expected. Sharing LCA results effectively builds trust, demonstrates accountability, and solidifies your brand as a leader in sustainability. Plan A helps you turn technical data into powerful narratives, driving stakeholder engagement and long-term success.
Communicating to B2B customers
Some strategies for effectively communicating LCA results with business customers include detailed reports, presentations, and collaborative initiatives.
- Detailed reports: Provide business customers with in-depth reports that outline the LCA findings, methodologies used, and implications for sustainability.
- Presentations: Conduct presentations for business partners to explain the LCA results and discuss potential collaboration on sustainability initiatives.
- Collaborative initiatives: Engage in joint sustainability projects with business customers, using LCA findings to identify areas for improvement and innovation.
Strategically integrating LCA into business operations offers significant benefits to businesses, including achieving regulatory compliance and gaining strategic advantage. Companies can also benefit from increased efficiency and reduced waste.
Most importantly, companies gain valuable insights that enable developing more sustainable and tailored products that align with evolving market and regulatory demands while improving environmental performance.
Since LCA processes can be complex and require comprehensive data collection and collaboration among various internal and external stakeholders, relevant technologies will be critical to conducting LCAs, integrating LCA data into other reporting requirements, and effectively communicating LCA results.
Your business can be part of the solution. Sign up for a free demo today and learn how Plan A can support your sustainability journey.